Canny property investor Sir Bob Jones’s announcement of his plan to build a tall timber building in Wellington reinforces timber’s claim to use in commercial buildings.
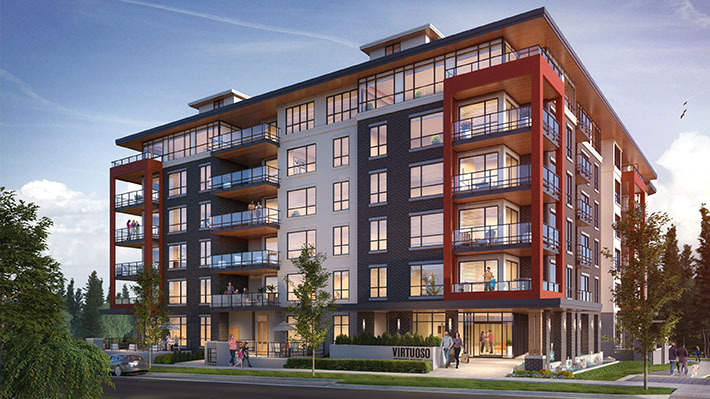
Render of the Virtuoso development in Vancouver, Canada © Adera.com
Jones has clearly done his homework on the advantages of wood for large commercial buildings, reflecting major overseas trends.
Australian and Canadian developers and building companies are well ahead of their New Zealand counterparts in using engineered wood to commercial advantage.
A recent announcement for another large building – a multi-family residential building, at the University of BC, in Vancouver Canada ( http://adera.com ) – saw the development company clarify why they chose wood for the project.
They said new engineered wood components like cross-laminated timber (CLT) meet or exceed the structural properties of concrete.
Wood components are seismically superior as they don’t crack or shatter like concrete.
Mass timber components are resistant to fire because the material self-chars, meaning oxygen can’t get at it.
It’s more sustainably produced, requires less energy to recycle, and since the panels are pre-assembled offsite, there’s virtually no on-site waste.
Quick construction
Quick construction is a highlight of CLT.
Cross-laminated timber panels weigh much less than concrete equivalents and are easily transported to their site for craning quickly into position.
Only two construction workers are needed to guide panels into place onto the building frame.
A typical floor for a multi-residential mid-rise building consists of 160 to 200 CLT panels.
They are lifted at a rate of one every 12 minutes.
The onsite crews erecting CLT panels can work at high rates – installing 400 m2 of floor space in less than three hours.
Brock Commons, currently the world’s tallest CLT building at 18 stories, was erected in nine weeks, at an average rate of two floors per week.
A national conference in Rotorua next month features as its keynote speaker the project manager from that building – Karla Fraser from Urban One Builders in Vancouver.
Silent assembly
The on-site assembly of engineered wood structures is also virtually silent — a definite bonus for the neighbours, say experienced managers like Fraser.
CLT construction is predicted to continue to make inroads as a viable, environmentally superior alternative to traditional “stick-on-stick” construction or concrete and steel design in the multi-family and high-rise market.
“One of the primary benefits of engineered wood structures is the way they influence design and scheduling,” Fraser explains.
“Unlike conventional construction, where you build the shear walls and then frame with plywood, CLT panels are tilted up and connect directly to the columns — a accurate method that’s simple, fast and very precise.”
As the market becomes more educated about the benefits of this product, demand will only continue to increase, Fraser predicts.
“There are so many benefits to using these materials for construction.
“It offers superior acoustic, fiber, seismic and thermal performance, not to mention a reduced carbon footprint.”
The upcoming national building industry conference, entitled “Changing Perceptions of Engineered Timber in Construction” runs on 28 September in Rotorua.
The diverse programme attracts building owners, developers, architects, engineers, specifiers and key engineered wood suppliers.
The conference theme is “Advantages of Timber in Mid Rise Construction”. For more details see: www.cpetc2017.com
The conference is set to be part of a wood technology week of events coming to the city in September, including the FIEA WoodTECH 2017 two-day conference and trade expo.
Rotorua Lakes Council are event partners promoting their successful “Wood-First” policy.